
Our Blog
Pool Installation Near Me Washingtonville, Blooming Grove, Orange County NY
Read feature stories and customer testimonials as well as news and updates from the world of fiberglass pools.
Subscribe
Sign up with your email address to receive news and updates
Search here for more ideas and inspiration.
-
July 2025
- Jul 1, 2025 How Expert Pool Contractors in Dobbs Ferry, NY Customize Plunge Pools for Outdoor Living Jul 1, 2025
-
June 2025
- Jun 2, 2025 How Professional Swimming Pool & Pool Design Enhances Weekend Living in Westchester County, NY Jun 2, 2025
-
May 2025
- May 8, 2025 Best Family-Friendly Fiberglass Pool Features in Carmel, NY and Putnam Valley, NY May 8, 2025
-
April 2025
- Apr 3, 2025 The Ultimate Swimming Pool Designs for Hosting in Warwick, NY: Features Pool Builders Recommend Apr 3, 2025
- March 2025
-
February 2025
- Feb 6, 2025 Custom Swimming Pools in Harrison and Westchester County, NY: Design Your Perfect Pool Feb 6, 2025
- January 2025
-
December 2024
- Dec 26, 2024 6 Custom Pool Designs Perfect for Relaxing Afternoon Lounges in Westchester County, NY Dec 26, 2024
- Dec 23, 2024 How to Choose the Right Pool Builders to Transform Your Backyard Into an Entertainment Hub in Fishkill, NY Dec 23, 2024
- Dec 11, 2024 Make Every Summer Special With a Family-Friendly Swimming Pool in Greene County and Eastchester, NY Dec 11, 2024
-
November 2024
- Nov 25, 2024 How Much Does a Fiberglass Pool Cost in Windham, NY? Unlock the Benefits of Affordable Luxury Nov 25, 2024
- Nov 18, 2024 Create the Ultimate Cool-Down Spot for Hot Summer Days With a Plunge Pool in Florida, NY and Ulster County, NY Nov 18, 2024
- Nov 7, 2024 4 Reasons to Start Your Swimming Pool Project This Fall in Hopewell Junction and Warwick, NY Nov 7, 2024
-
October 2024
- Oct 28, 2024 Enjoy Luxurious Evening Swims in a Luxurious Swimming Pool for Your Scarsdale, NY, Backyard Oct 28, 2024
- Oct 23, 2024 How a Plunge Pool in West Point and Hunter, NY, Can Become the Heart of Your Family’s Outdoor Experience Oct 23, 2024
- Oct 3, 2024 5 Ways Pool Installation in Greene County, NY, Turns Your Backyard Into the Perfect Hub for Family Gatherings Oct 3, 2024
-
September 2024
- Sep 27, 2024 Staycation Perfection: How Fishkill, NY Pool Builders Create the Ultimate Backyard Resort Experience Sep 27, 2024
- Sep 18, 2024 Ways Your East Chester or Fishkill, NY Swimming Pool Can Be Your Ultimate Stress Relief Sanctuary Sep 18, 2024
- Sep 5, 2024 Barbecues With a Splash in Hunter, NY: How Your Inground Pool Elevates Outdoor Parties Sep 5, 2024
-
August 2024
- Aug 20, 2024 How Swim-Up Bars Enhance Backyard Pools in Bedford Hills and Lagrangeville, NY Aug 20, 2024
- Aug 12, 2024 Discover the Serenity of Waterfalls in Your Woodbury, NY Freeform Inground Pool Aug 12, 2024
- Aug 6, 2024 Luxury Infinity Pool Designs in Bedford Hills, NY: What to Expect From Top Pool Companies Aug 6, 2024
-
July 2024
- Jul 26, 2024 Expert Pool Installation Services in Scarsdale, NY: Step-by-Step to Your Dream Pool Jul 26, 2024
- Jul 11, 2024 The Art of Pool Design in Westchester County, NY: Creating Spaces for Relaxation and Entertainment Jul 11, 2024
- Jul 2, 2024 Discover Premier Pool Services: Selecting the Best Pool Companies in Ulster County, NY Jul 2, 2024
-
June 2024
- Jun 25, 2024 Exploring Inground Pool Options With Top Pool Companies in Briarcliff Manor, NY Jun 25, 2024
- Jun 17, 2024 Seamless Pool Installation Services in Ulster County & Briarcliff Manor, NY: What to Expect Jun 17, 2024
- Jun 6, 2024 Transformative Pool Designs for Luxurious Outdoor Living in Westchester County and Bedford, NY Jun 6, 2024
-
May 2024
- May 25, 2024 Choosing the Right Inground Pool and Pool Companies in Ulster County, NY: A Guide for Homeowners May 25, 2024
- May 14, 2024 Dive Into Luxury: Explore Fiberglass Pool Designs for Your Florida, NY Residence May 14, 2024
- May 2, 2024 Elevate Your Outdoor Living: Why Backyard Pools Are Your Next Big Home Upgrade in Bedford Hills, NY May 2, 2024
-
April 2024
- Apr 18, 2024 The Secret to Creating the Ultimate Pool Design in Westchester County and Scarsdale, NY Apr 18, 2024
- Apr 9, 2024 8 Surprising Ways Backyard Pools Can Improve Your Life in Orange County, NY Apr 9, 2024
- Apr 4, 2024 Transform Your Ulster County, NY Backyard with a Pool Design From Expert Pool Companies Apr 4, 2024
-
March 2024
- Mar 26, 2024 Bring Luxury to Your Backyard With Inground Pools in Carmel and Dobbs Ferry, NY Mar 26, 2024
- Mar 17, 2024 Elevate Your Outdoor Space With Unique Pool Designs in Florida and Eastchester, NY Mar 17, 2024
- Mar 7, 2024 Why Woodbury, NY Homes Are Choosing Custom Backyard Pools for Summer Fun Mar 7, 2024
-
February 2024
- Feb 29, 2024 Learn What to Look for in 'Pool Installation Near Me' and 'Pool Companies Near Me' in Carmel, NY Feb 29, 2024
- Feb 19, 2024 Why Residents in Orange County and Ulster County, NY Are Opting for an Inground Pool Feb 19, 2024
- Feb 9, 2024 What to Know When Searching for the Perfect Pool Design in Westchester County and Scarsdale, NY Feb 9, 2024
-
January 2024
- Jan 31, 2024 Enhancing Your Landscape With Perfect Pool Design: A Guide To Harmonious Outdoor Living in Scarsdale and Eastchester, NY Jan 31, 2024
- Jan 20, 2024 Build a Backyard Oasis with a Fiberglass Pool in Caramel and Monroe, NY Jan 20, 2024
- Jan 10, 2024 How Pool Companies Near Me Build the Ideal Inground Pool in Ulster County, NY Jan 10, 2024
-
December 2023
- Dec 27, 2023 Enhance Your Scarsdale, NY Home with an Elegant Inground Pool: A Guide to Choices and Styles Dec 27, 2023
- Dec 17, 2023 Explore Stunning Inground Pool Designs in Ulster County, NY to Transform Your Backyard Dec 17, 2023
- Dec 6, 2023 How Transforming Your Outdoor Space with Backyard Pool Companies Near Me in Orange County, NY Can Elevate Your Home Dec 6, 2023
-
November 2023
- Nov 30, 2023 Planning a New Carmel, NY Outdoor Space? Search Backyard Pools Near Me for Inspiration Nov 30, 2023
- Nov 14, 2023 Confused by Backyard Pool Designs? Let a Westchester County, NY Pool Company Create Your Dream Nov 14, 2023
- Nov 4, 2023 Interested in an Inground Pool? Search Inground Pool Companies Near Me for Luxurious Briarcliff Manor, NY Designs Nov 4, 2023
-
October 2023
- Oct 23, 2023 Small Briarcliff Manor or Scarsdale, NY Backyard? Check for Plunge Pool Installations Near Me Oct 23, 2023
- Oct 16, 2023 Need Ideas for an Inground Pool Project? Search for Briarcliff Manor, NY Pool Companies Near Me Oct 16, 2023
- Oct 9, 2023 Struggling With a Westchester County or Orange County, NY Pool Design? Let a Pool Specialist Help! Oct 9, 2023
-
September 2023
- Sep 27, 2023 How to Make the Most of an Inground Pool Experience in the Hamptonburgh and Bedford Hills, NY Areas Sep 27, 2023
- Sep 22, 2023 Discover the Versatility of Backyard Pools in the Hamptonburgh and Rye Brook, NY Areas Sep 22, 2023
- Sep 13, 2023 Why Fiberglass Inground Pools are a Must-Have for Modern Homes in the Irvington and Washingtonville, NY Areas Sep 13, 2023
-
August 2023
- Aug 30, 2023 What Pool Companies Near Me Recommend for a Relaxing Poolscape in the Briarcliff Manor and Bedford, NY Areas Aug 30, 2023
- Aug 22, 2023 Which Pool Design, Shape, and Style Best Fits Your Lifestyle in the Bedford and Westchester County, NY Areas? Aug 22, 2023
- Aug 8, 2023 Dreaming of Backyard Pools? How an Inground Pool Can Be Life-Changing in Hamptonburgh, NY Aug 8, 2023
-
July 2023
- Jul 26, 2023 Factors That Influence Fiberglass Pool Cost in a Search of "Pool Installation Near Me" in the Washingtonville, NY Area Jul 26, 2023
- Jul 21, 2023 Clever Pool Design Options to Consider for a New Inground Pool in the Larchmont, NY Area Jul 21, 2023
- Jul 14, 2023 Maintenance for Backyard Pools: Tips for Caring for Your Fiberglass Pool in the Washingtonville, NY Area Jul 14, 2023
-
June 2023
- Jun 27, 2023 Backyard Pools for Exercise, Health, and Other Benefits of Swimming at Home in the Ulster County and Bedford Hills, NY Areas Jun 27, 2023
- Jun 20, 2023 A Quick Checklist of What to Look For in “Pool Companies Near Me” in the Pleasantville and Harrison, NY Areas Jun 20, 2023
- Jun 13, 2023 From Elegant to Cozy: How to Choose the Perfect Pool Design for Your Backyard in the Scarsdale and Westchester County, NY Areas Jun 13, 2023
-
May 2023
- May 23, 2023 How to Choose the Best Pool Design for Your Backyard: A Guide to Pool Installation Near Me in the Scarsdale, NY Area May 23, 2023
- May 16, 2023 The Benefits of Owning an Inground Pool: Health, Entertainment, and More in the Monroe and Briarcliff Manor, NY Areas May 16, 2023
- May 9, 2023 Why Working with Experienced Pool Companies Near Me in the Bedford and Scarsdale, NY Areas Is Recommended May 9, 2023
-
April 2023
- Apr 25, 2023 Here’s How You Know You’ve Made the Right Choice From “Pool Companies Near Me” in the Washingtonville and Bedford, NY Areas Apr 25, 2023
- Apr 18, 2023 Choose a Custom Pool Design to Get the Features You Want in Your Inground Pool in the Briarcliff Manor, NY Area Apr 18, 2023
- Apr 11, 2023 Top Advice From Pool Companies Near Me: How to Get the Best Pool for Your Lifestyle in the Pleasantville and Scarsdale, NY Areas Apr 11, 2023
-
March 2023
- Mar 28, 2023 What to Look for in Your Search of “Pool Installation Near Me” in Hastings-on-Hudson and Washingtonville, NY Areas Mar 28, 2023
- Mar 21, 2023 Pool Design Ideas to Consider After Looking for “Pool Installation Near Me” in the Scarsdale, NY Area Mar 21, 2023
- Mar 7, 2023 Recommendations From Pool Companies Near Me for a Backyard Made for Entertaining in the Briarcliff Manor, NY, Area Mar 7, 2023
-
February 2023
- Feb 27, 2023 4 Unique Pool Design Ideas for Very Active Backyard Pools in the Cornwall, NY, Area Feb 27, 2023
- Feb 17, 2023 How to Choose the Right Professionals for Your Inground Pool in Your Search for “Pool Installation Near Me” in the Jefferson Valley, NY, Area Feb 17, 2023
- Feb 7, 2023 Have Your Eyes on an Inground Pool? Here Are Options Provided by Pool Companies Near Me in the Carmel, NY, Area Feb 7, 2023
-
January 2023
- Jan 24, 2023 Endless Customizable Options Provided by a Pool Installation Company Near Me in the Jefferson Valley and Briarcliff Manor, NY, Areas Jan 24, 2023
- Jan 17, 2023 Is an Inground Pool a Fit for Your Unique Backyard in the Rye Brook and Scarsdale, NY, Areas? Jan 17, 2023
- Jan 10, 2023 Dreaming of Poolside Living? Here’s How Searching “Pool Installation Near Me” Can Start the Process in the Harrison and Cornwall, NY, Areas Jan 10, 2023
-
December 2022
- Dec 28, 2022 Here Are 3 Backyard Pools Perfect for Entertaining in the Rye Brook and Scarsdale, NY, Areas Dec 28, 2022
- Dec 20, 2022 6 Quick Tips for Planning a Pool Design in the Harrison, NY, Area From Pool Companies Near Me Dec 20, 2022
- Dec 6, 2022 Here’s What Pool Companies Near Me Recommend for a Low Maintenance, Durable Inground Pool in the Scarsdale and Orange County, NY, Areas Dec 6, 2022
-
November 2022
- Nov 23, 2022 A Look at What Is Included in Fiberglass Pool Cost in the Woodbury, NY, Area Nov 23, 2022
- Nov 15, 2022 An Inground Pool Is Just a Quick Search Away From “Pool Installation Near Me” in the Rye, NY, Area Nov 15, 2022
- Nov 4, 2022 Hiring a Company That Uses 3D Pool Design Software Is the Best Way to Bring Your Full Vision to Life in Westchester County and Ulster County, NY Nov 4, 2022
-
October 2022
- Oct 28, 2022 Here Are 5 Inground Pool Models to Consider in the Rye Brook, NY, Area Oct 28, 2022
- Oct 20, 2022 Why Are Backyard Pools Worth It in the Scarsdale, NY, Area? Oct 20, 2022
- Oct 6, 2022 5 Things You Should Know Before Contacting Pool Companies Near Me in the Bronxville, NY Area Oct 6, 2022
-
September 2022
- Sep 28, 2022 A Customized Pool Design Is Key to Making the Most of Your Harrison, NY, Backyard Sep 28, 2022
- Sep 20, 2022 Searching “Pool Installation Near Me” Is a Great Way to Find Inspiration in the Bedford, NY, Area Sep 20, 2022
- Sep 12, 2022 Looking for a Uniquely Shaped Inground Pool in the Bedford, NY, Area? Gunite Could Be Your Best Option Sep 12, 2022
-
August 2022
- Aug 29, 2022 Dreamscapes: Here Is How Pool Companies Near Me Envision Beautiful Pool Areas in Hamptonburgh, NY Aug 29, 2022
- Aug 17, 2022 Fully Customize Your Landscape with Ideas for Gunite Backyards Pools in Carmel, NY Aug 17, 2022
- Aug 9, 2022 4 Ideas for a Low-Maintenance Pool Design in the Bedford, NY, Area Aug 9, 2022
-
July 2022
- Jul 28, 2022 Searching “Pool Installation Near Me” and Not Sure If You Have The Right Backyard for a Pool? A Retaining Wall Can Help in Briarcliff Manor, NY Jul 28, 2022
- Jul 18, 2022 3 Benefits of Choosing Pool Companies Near Me That Use 3D Design in Harrison, NY Jul 18, 2022
- Jul 7, 2022 6 Reasons to Add an Outdoor Kitchen Alongside Your Inground Pool in Rye and Carmel, NY Jul 7, 2022
-
June 2022
- Jun 28, 2022 7 Fun Additions for Your Dutchess County and Briarcliff Manor, NY, Pool Design Jun 28, 2022
- Jun 17, 2022 These 3 Styles Are Favorites Among Pool Companies Near Me in Carmel and Woodbury, NY Jun 17, 2022
- Jun 6, 2022 7 Color Options for Backyard Pools in Ulster County, NY Jun 6, 2022
-
May 2022
- May 27, 2022 Why Pool Companies Near Me Recommend Installing a Fiberglass Pool in Carmel, NY May 27, 2022
- May 18, 2022 A Look Into Shapes: What Your Options Are for Your Bronxville and Rye, NY, Pool Design May 18, 2022
- May 6, 2022 Make Your House The Entertainment Hub This Summer With an Inground Pool in Orange County and Ulster County, NY May 6, 2022
-
April 2022
- Apr 28, 2022 Searching “Pool Installation Near Me” Can Help You Know What to Expect With Your Pool Design in Carmel, NY Apr 28, 2022
- Apr 18, 2022 Enjoy More Family Time This Summer With These Ideas for Backyard Pools in Orange County and Rye, NY Apr 18, 2022
- Apr 8, 2022 What Pool Companies Near Me Suggest When Choosing Between a Fiberglass and Gunite Pool in Bedford and Carmel, NY Apr 8, 2022
-
March 2022
- Mar 28, 2022 Pool Design Options for Smaller Backyards in Eastchester and Orange County, NY Mar 28, 2022
- Mar 18, 2022 Looking at Installing a Pool? Here Is What You Can Expect for Fiberglass Pool Cost in Dobbs Ferry, NY Mar 18, 2022
- Mar 8, 2022 Here Are 3 Ideas for Additions to an Inground Pool in Dobbs Ferry and Carmel, NY Mar 8, 2022
-
February 2022
- Feb 23, 2022 Consider These 6 Pool Design Ideas When Looking For Pool Installation Near Me in Carmel, NY Feb 23, 2022
- Feb 14, 2022 Want to Get the Most Out of Your Pool? 5 Additions That Can be Added to Backyard Pools in Bedford and Pleasantville, NY Feb 14, 2022
- Feb 7, 2022 Searching “Pool Installation Near Me” Now Can Beat the Rush of Planning Your 2022 Pool Design in Lagrangeville, NY Feb 7, 2022
-
January 2022
- Jan 27, 2022 Why a Fiberglass Pool Could Be the Best Option for Your Inground Pool in Ulster County, NY Jan 27, 2022
- Jan 21, 2022 Searching “Pool Companies Near Me” Is a Great Way to Find Inspiration in Lagrangeville and Highland Mills, NY Jan 21, 2022
- Jan 6, 2022 4 Inground Pool Ideas That Are a Perfect Fit for Any Backyard in Rye and Bedford Hills, NY Jan 6, 2022
-
December 2021
- Dec 23, 2021 Pool Companies Near Me May Suggest These Additions to a New Inground Pool in Scarsdale, NY Dec 23, 2021
- Dec 16, 2021 Options for Backyard Pools: Here Is Why a Fiberglass Pool Should Be at the Top of Your List in Carmel, NY Dec 16, 2021
- Dec 6, 2021 Searching for “Pool Installation Near Me” Is a Great Start When Planning a New Pool in Harrison and Rye, NY Dec 6, 2021
-
November 2021
- Nov 24, 2021 Pool Companies Near Me Recommend These 3 Pool Designs in Ulster County, NY Nov 24, 2021
- Nov 18, 2021 Ideas for Backyard Pools: Get the Most Out of Your Highland Mills and Larchmont, NY, Pool With These Features Nov 18, 2021
- Nov 5, 2021 Looking at Adding an Inground Pool? Why Pool Companies Near Me Suggest Getting on the List Now in Carmel, NY Nov 5, 2021
-
October 2021
- Oct 27, 2021 Reasons Why a Fiberglass Inground Pool Is a Top Choice for Backyard Pools in Lagrangeville, NY Oct 27, 2021
- Oct 19, 2021 After the Search for Pool Installation Near Me, Here Is What to Expect for Your Pool Project in Orange County, NY Oct 19, 2021
- Oct 6, 2021 Why the Cooler Season Could Be the Best Time to Look Into Pool Companies Near Me for an Inground Pool in Irvington, NY Oct 6, 2021
-
September 2021
- Sep 27, 2021 Searching for a New Pool Installation Near Me In Ulster County, NY? Include These 6 Customizations Sep 27, 2021
- Sep 22, 2021 Featured In: Vents Magazine Sep 22, 2021
- Sep 19, 2021 5 Ways to Extend the Use of Your Inground Pool in Pelham and Larchmont, NY Sep 19, 2021
- Sep 8, 2021 Pool Companies Near Me Suggest These 4 Pool Design Ideas in Irvington, NY Sep 8, 2021
-
August 2021
- Aug 27, 2021 How Time-Consuming Is a Pool Installation Near Me in Carmel and Hamptonburgh, NY? Aug 27, 2021
- Aug 17, 2021 What You Should Know About Fiberglass Pool Cost in Briarcliff Manor and Bedford Hills, NY Aug 17, 2021
- Aug 9, 2021 4 Pool Design Features You'll Want to Include With Your Woodbury, NY, Inground Pool Aug 9, 2021
-
July 2021
- Jul 27, 2021 Pool Companies Near Me Suggest These 5 Tips When Planning an Inground Pool in the Harrison, NY, Area Jul 27, 2021
- Jul 15, 2021 Looking at Backyard Pools? Here’s How Long a Pool Installation Near Me Takes in Dobbs Ferry, NY Jul 15, 2021
- Jul 7, 2021 When a Fiberglass Pool Is the Best Choice for an Inground Pool in Hastings-on-Hudson, NY Jul 7, 2021
-
June 2021
- Jun 27, 2021 Inspired to Swim: What to Look For in a Pool Installation Near Me in Pleasantville, NY Jun 27, 2021
- Jun 16, 2021 Pool Companies Near Me Suggest Adding These Options to an Inground Pool in Carmel, NY Jun 16, 2021
- Jun 7, 2021 5 Pool Design Ideas That Maximize the View in the Harrison and Bedford, NY, Areas Jun 7, 2021
-
May 2021
- May 26, 2021 Pool Companies Near Me Suggest These Amenities for Pool Fun in the Jefferson Valley, NY Area May 26, 2021
- May 16, 2021 4 Ideas to Improve the Look of Backyard Pools in Hastings-on-Hudson and Carmel, NY, Homes May 16, 2021
- May 6, 2021 5 Pool Design Trends That Could Work With Any Landscape in Dutchess County and Westchester County, NY May 6, 2021
-
April 2021
- Apr 26, 2021 What Is the Process of Pool Installation Near Me for Scarsdale, NY, Backyard Pools? Apr 26, 2021
- Apr 16, 2021 5 Pool Design Ideas for a Frequently Enjoyed Inground Pool in the Croton-on-Hudson, NY, Area Apr 16, 2021
- Apr 6, 2021 How Do Pool Companies Near Me Create Stunning Backyard Pools in Beekman, NY? Apr 6, 2021
-
March 2021
- Mar 28, 2021 Essential Features for Making Backyard Pools Kid-Friendly in Bedford and Armonk, NY Mar 28, 2021
- Mar 18, 2021 How Much Does a Fiberglass Pool Installation Cost Near Me in Florida, NY? Mar 18, 2021
- Mar 8, 2021 Choosing a Pool Design in Hastings-on-Hudson and Briarcliff Manor, NY? Keep These Tips in Mind Mar 8, 2021
-
February 2021
- Feb 28, 2021 4 Ideas for Dramatic Pools That Transform Any Backyard in Dobbs Ferry, NY, and Rye Brook, NY, Areas Feb 28, 2021
- Feb 19, 2021 How to Draw Inspiration From a Pool Installation Near Me in Orange County, NY Feb 19, 2021
- Feb 9, 2021 Using Water Features to Take Your Inground Pool to the Next Level in the Wawayanda and Bedford Hills, NY, Areas Feb 9, 2021
-
January 2021
- Jan 29, 2021 Inground Pool Design Ideas for Every Type of Outdoor Living Space in Croton-on-Hudson and Greenville, NY Jan 29, 2021
- Jan 19, 2021 3 Low-Maintenance Hacks for Backyard Pools in Hamptonburgh and Woodbury, NY, Areas Jan 19, 2021
- Jan 9, 2021 How Pool Companies Near Me Visually Connect the Pool to the Home in Pelham and Bedford Hills, NY, Areas Jan 9, 2021
-
December 2020
- Dec 30, 2020 5 Trending Pool Design Options for Relaxing Backyard Pools in Ulster County, NY Dec 30, 2020
- Dec 20, 2020 When Are Fiberglass Inground Pools the Way to Go in Woodbury and Florida, NY, Areas? Dec 20, 2020
- Dec 10, 2020 How Pool Companies Near Me Customize Pool Installation in Pelham, NY Dec 10, 2020
-
November 2020
- Nov 30, 2020 3 Signs an Inground Pool Would Be a Good Fit for Your Backyard in Lagrangeville, Dutchess County, NY Nov 30, 2020
- Nov 24, 2020 10 Reasons to Opt for Fiberglass Inground Pools in West Point and Highland Mills, NY, Areas Nov 24, 2020
- Nov 15, 2020 How Pool Companies Near Me Customize Swimming Pools in Briarcliff Manor, Westchester County, NY Nov 15, 2020
-
March 2018
- Mar 30, 2018 9 easy steps to close and winterize your fiberglass pool Mar 30, 2018
- Mar 30, 2018 5 reasons why our customer Lou chose a fiberglass swimming pool Mar 30, 2018
- Mar 15, 2018 7 Reasons to LOVE a Fiberglass Pool : Albert Group Landscaping and Swimming Pools Review Mar 15, 2018
-
April 2017
- Apr 4, 2017 Creating Beautiful Backyards and Happy Clients - Project Spotlight #1 Apr 4, 2017
-
April 2016
- Apr 11, 2016 5 Benefits of Fiberglass Swimming Pools Apr 11, 2016
-
February 2016
- Feb 21, 2016 Fiberglass Swimming Pool Builder, Westchester County, Somers, NY Feb 21, 2016
-
March 2014
- Mar 30, 2014 Pros and Cons of 3 Types of Retaining Walls Mar 30, 2014
-
March 2013
- Mar 6, 2013 7 problems with Gunite pools that you need to know. Mar 6, 2013
-
February 2013
- Feb 5, 2013 What type of retaining wall do I need? Feb 5, 2013
- Feb 2, 2013 Why do fiberglass pools crack? Feb 2, 2013
- Feb 1, 2013 Are fiberglass swimming pools any good? Feb 1, 2013
-
January 2013
- Jan 16, 2013 Does any company make a Carbon Fiber Swimming Pool? Jan 16, 2013
- Jan 11, 2013 New Research to Prove Health Benefits of Swimming Pools Jan 11, 2013
-
December 2012
- Dec 18, 2012 Why You Should Order Your Swimming Pool Now Dec 18, 2012
- Dec 14, 2012 How to Use Walkways and Retaining Walls to Create Winter-Magic Dec 14, 2012
-
November 2012
- Nov 22, 2012 Hardscape: How to Maintain a Safe Walkway through the Winter Nov 22, 2012
- Nov 5, 2012 How to Avoid Retaining Wall Failures Nov 5, 2012
-
October 2012
- Oct 26, 2012 How to Increase Your Livingspace with Retaining Walls Oct 26, 2012
- Oct 12, 2012 How to Care for your Retaining Wall Oct 12, 2012
-
August 2012
- Aug 25, 2012 Outdoor Living Trends for 2012 Aug 25, 2012
- Aug 18, 2012 What Types of Material are Best for Retaining Walls? Aug 18, 2012
- Aug 11, 2012 What is the most durable retaining wall? Aug 11, 2012
- Aug 4, 2012 Can I Work Out in the Swimming Pool? Aug 4, 2012
- Aug 1, 2012 What Water Features Can Be Installed With Fiberglass Pools? Aug 1, 2012
-
July 2012
- Jul 28, 2012 How to Beautify your Swimming Pool Jul 28, 2012
- Jul 25, 2012 What you always wanted to know about Swimming Pools Jul 25, 2012
- Jul 21, 2012 Can I build a Swimming Pool in a Small Yard? Jul 21, 2012
- Jul 17, 2012 Backyard Swimming Pool Vacation: Go Global Jul 17, 2012
- Jul 12, 2012 Should I Buy a Swimming Pool? Jul 12, 2012
- Jul 11, 2012 How to Have the best Swimming Pool Party Jul 11, 2012
- Jul 8, 2012 Are Fiberglass Pools Heat Resistant? Jul 8, 2012
- Jul 7, 2012 Heat wave: How to stay cool in the swimming pool Jul 7, 2012
-
June 2012
- Jun 29, 2012 Swimming Pool Games for 4th of July Jun 29, 2012
- Jun 27, 2012 Which Decking Option should I choose for my Fiberglass Pool? Jun 27, 2012
- Jun 25, 2012 What to consider when you get a Swimming Pool Jun 25, 2012
- Jun 23, 2012 Why a Fiberglass Pool is the perfect choice for your Weekend Home Jun 23, 2012
- Jun 20, 2012 Albert Group Landscaping: What is the Difference? Jun 20, 2012
- Jun 12, 2012 Swimming Pools: Health Benefits for Children with Asthma Jun 12, 2012
- Jun 12, 2012 Swimming Pool Landscaping for a Cleaner Environment Jun 12, 2012
- Jun 9, 2012 Weekend Home With Swimming Pool Jun 9, 2012
- Jun 8, 2012 Swimming Pool: 10 Year Cost Projection Jun 8, 2012
- Jun 6, 2012 Swimming Pools: A Great Addition for Weekend Homes Jun 6, 2012
- Jun 5, 2012 Should I add a swimming pool to my weekend house? Jun 5, 2012
- Jun 5, 2012 Natural Landscaping Ideas Jun 5, 2012
- Jun 3, 2012 Inground Swimming Pools: Preferred Qualities Jun 3, 2012
- Jun 1, 2012 Retaining Walls: Made to Fit Your Dreams Jun 1, 2012
-
May 2012
- May 30, 2012 Swimming Pools: How to Choose the Location May 30, 2012
- May 26, 2012 Swimming Pool: Health Benefits of Water Workouts May 26, 2012
- May 26, 2012 Fiberglass Swimming Pools for Small Yards May 26, 2012
- May 24, 2012 Swimming Pool Fitness: Get the Most out of your Laps May 24, 2012
- May 23, 2012 Swimming Pool Landscaping Ideas May 23, 2012
- May 22, 2012 Health Benefits of Swimming Pools May 22, 2012
- May 19, 2012 Swimming Pool Landscaping: What plants to avoid May 19, 2012
- May 18, 2012 Swimming Pool Apps for your Smartphone May 18, 2012
- May 17, 2012 Swimming Pool “Must haves” May 17, 2012
- May 16, 2012 Swimming Pool Construction: Why a Building Permit is Important May 16, 2012
- May 15, 2012 Swimming Pool Safety: Why maintanance is important May 15, 2012
- May 14, 2012 Swimming Pool Savings: New App to Calculate Cost of Energy and Water May 14, 2012
- May 12, 2012 Swimming Pool Heaters: The Right Option for You May 12, 2012
- May 11, 2012 Swimming Pool Options for Small Yards May 11, 2012
- May 9, 2012 Does a Swimming Pool Increase the Home Value? May 9, 2012
- May 8, 2012 Retaining Walls: How to integrate them in your Swimming Pool Area May 8, 2012
- May 7, 2012 Swimming Pools: Why You Should Consider a Water Feature May 7, 2012
- May 4, 2012 Inground Pools on Sloped Yard: 5 Ways to build May 4, 2012
- May 3, 2012 Fiberglass Swimming Pool Surfaces - The Benefits May 3, 2012
- May 2, 2012 Swimming Pool Parties: Games for Kids May 2, 2012
- May 1, 2012 Inground Swimming Pools: What is the Best Kind Of Lighting? May 1, 2012
-
April 2012
- Apr 30, 2012 Salt Chlorine Generators: The Benefit of a Healthier Swimming Pools Apr 30, 2012
- Apr 27, 2012 How to detect a leak in your swimming pool? Apr 27, 2012
- Apr 26, 2012 Outdoor Waterfeatures Increase the Home Value Apr 26, 2012
- Apr 24, 2012 Stamped Concrete: The best option for Swimming Pool Decks Apr 24, 2012
- Apr 22, 2012 Cool Workouts for the Swimming Pool Apr 22, 2012
- Apr 17, 2012 Go Green: Environmentally Friendly Swimming Pools Apr 17, 2012
- Apr 15, 2012 Fun in the swimming pool: Games that teach confidence Apr 15, 2012
- Apr 14, 2012 Why Fiberglass Pools are better Apr 14, 2012
- Apr 10, 2012 Leisure Pool Award for Albert Group Landscaping Apr 10, 2012
- Apr 6, 2012 Swimming Pools: Summer vacation in the back yard Apr 6, 2012
- Apr 4, 2012 Pool covers: The new smart choice for savings and safety Apr 4, 2012
- Apr 2, 2012 Pool Safety Check: Features worth their money Apr 2, 2012
-
July 2011
- Jul 21, 2011 Concrete Block Alternative Jul 21, 2011
- Jul 20, 2011 What you can visualize, we can realize with StoneMakers Jul 20, 2011
- Jul 15, 2011 StoneMakers vs. Concrete Pavers Jul 15, 2011
- Jul 13, 2011 Patios, Walkways, Waterfalls and Walls Installed in Days Not Weeks Jul 13, 2011
- Jul 11, 2011 Beautify your Home with an Affordable Concrete Block Alternative Jul 11, 2011
- Jul 11, 2011 Why the StoneMakers Product Costs less than Traditional Concrete Jul 11, 2011
-
June 2011
- Jun 8, 2011 Seven Reasons to Consider a Backyard Water Feature Jun 8, 2011
-
May 2011
- May 30, 2011 Five Popular Outdoor Hardscape Projects May 30, 2011
- May 27, 2011 Natural Stone Adds to the Value of your Home May 27, 2011
- May 25, 2011 Why StoneMakers is Stronger than Normal Concrete May 25, 2011
-
April 2011
- Apr 6, 2011 Are fiberglass pools too slippery for comfort? Apr 6, 2011
-
March 2011
- Mar 25, 2011 Albert Group Landscaping and Swimming Pools will be at the Orange County Home Show! Mar 25, 2011
- Mar 19, 2011 Swimming pool buying advice - Download our free e-book now! Mar 19, 2011
- Mar 9, 2011 Insights as to why retaining walls fail – Part 2 Mar 9, 2011
-
February 2011
- Feb 27, 2011 Insights as to why retaining walls fail – Part 1 Feb 27, 2011
- Feb 23, 2011 5 ways StoneMakers retaining walls have changed the industry FOREVER Feb 23, 2011
- Feb 21, 2011 Home Show Specials on All Swimming Pools and Landscaping, March 4,5,6 Feb 21, 2011
- Feb 17, 2011 Why a vinyl liner pool costs less than fiberglass – you get less. Feb 17, 2011
- Feb 16, 2011 Why spending more on a high efficiency pool pump will save you money. Feb 16, 2011
- Feb 15, 2011 A dozen spring plants to make your flower garden explode with color! Feb 15, 2011
- Feb 14, 2011 Top 5 questions people ask when buying a retaining wall. Feb 14, 2011
- Feb 12, 2011 5 Reasons the ownership experience of a Fiberglass Pool is awesome! Feb 12, 2011
- Feb 11, 2011 8 Tips to make your next paver job turn out great! Pavers done right! Feb 11, 2011
- Feb 10, 2011 5 Reasons why NOW is the best time to buy your inground swimming pool Feb 10, 2011
- Feb 4, 2011 3D Landscape and Pool design, You only have one shot to get it right! Feb 4, 2011
-
December 2010
- Dec 27, 2010 5 reasons why StoneMakers Concrete is the best choice for your new patio Dec 27, 2010
- Dec 21, 2010 StoneMakers Skeptic Turned Believer - Concrete walls without forms!?! Dec 21, 2010
- Dec 16, 2010 Albert Group Landscaping & Swimming Pools - StoneMakers newest Dealer Dec 16, 2010
- Dec 11, 2010 Albert Group Landscaping Featured in upcoming Issue of Pool & Spa News Dec 11, 2010
- Dec 6, 2010 Bring the indoors outside by adding an Outdoor Kitchen. Dec 6, 2010
-
November 2010
- Nov 21, 2010 Check out our new Holiday Giveaway Nov 21, 2010
-
October 2010
- Oct 10, 2010 How does a fiberglass pool get delivered to my home? Oct 10, 2010
-
September 2010
- Sep 28, 2010 How to Install fittings in a fiberglass pool Sep 28, 2010
- Sep 26, 2010 Top 5 questions people ask when buying a fiberglass pool Sep 26, 2010
-
May 2010
- May 9, 2010 5 reasons fiberglass pools are are great in northeast climates May 9, 2010
-
April 2010
- Apr 13, 2010 What type of pool filter is best? Apr 13, 2010
- Apr 13, 2010 How to find the right in ground swimming pool. Apr 13, 2010
- Apr 10, 2010 Albert Group Landscaping’s landscape design department utilizes a 3D virtual tour for your custom designed landscape and pool projects. Apr 10, 2010
- Apr 1, 2010 Three great plants for your shade garden. Apr 1, 2010
- Apr 1, 2010 What makes Leisure Pools USA different from the competition? Apr 1, 2010
-
March 2010
- Mar 28, 2010 Video of a project from start to finish - Albert Group Landscaping Installs a retaining wall and walkway. Mar 28, 2010
- Mar 25, 2010 How do you make a corner when building a retaining wall? Mar 25, 2010
- Mar 21, 2010 Why hire a landscape company to design and construct your pool? Mar 21, 2010
- Mar 20, 2010 What are the pros and cons of a vinyl liner pool? Mar 20, 2010
- Mar 17, 2010 How do you cut pavers? Mar 17, 2010
- Mar 17, 2010 How do I close my in-ground swimmming pool? Mar 17, 2010
- Mar 6, 2010 What is better? - Pavers vs. Concrete Mar 6, 2010
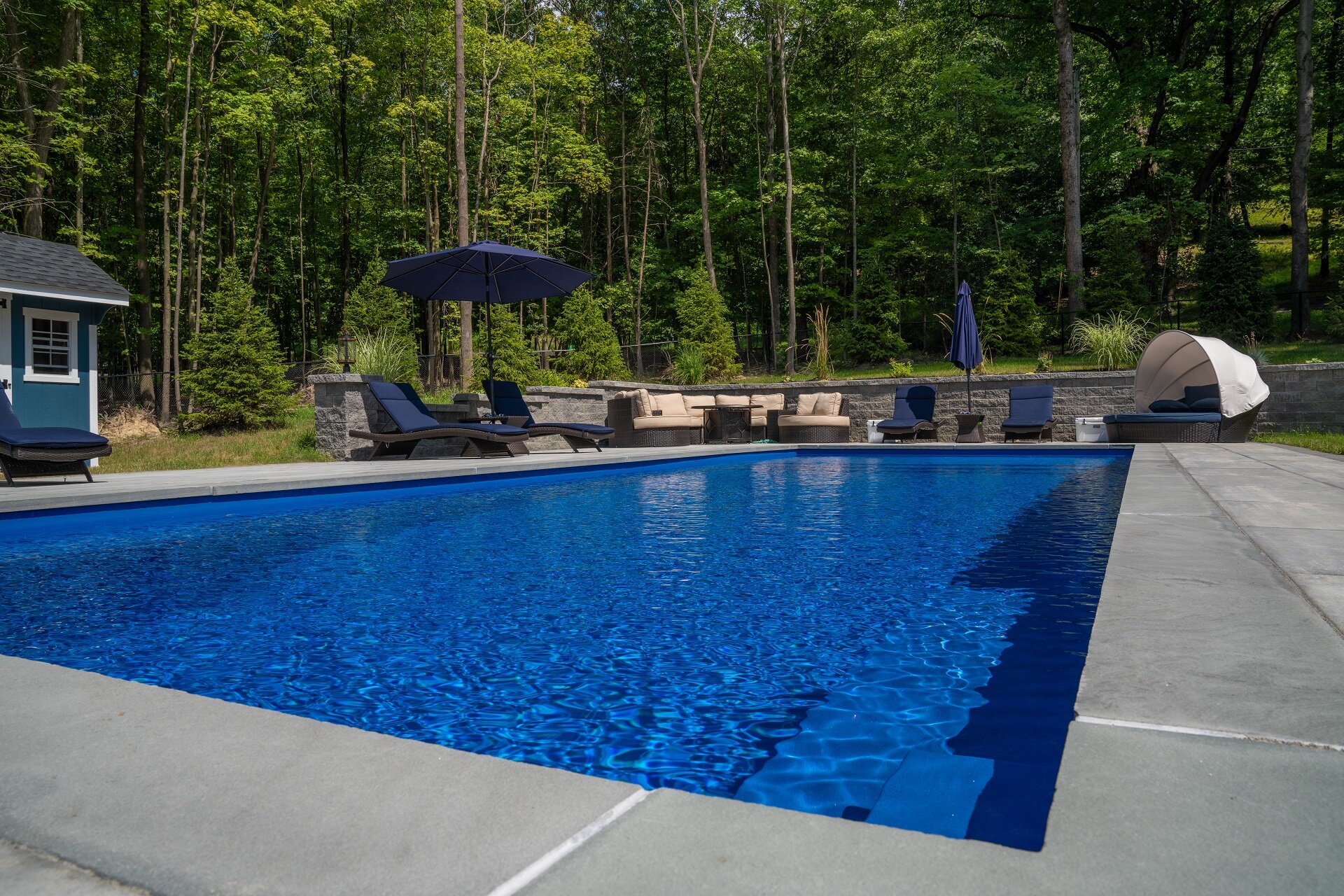
Leading pool companies near me Washingtonville, Blooming Grove, Orange County NY